the thinair 102 wind turbine
Quiet, Efficient, Affordable Domestic Wind Power
The Thinair 102 wind turbine is pioneering development of Powerhouse Wind, and is designed to be a component of an off-grid renewable energy system or micro-grid. Its generation profile is compatible with that of solar panels as it is will continue to generate power at night and during the shorter cloudy winter days.
IMPORTANT: We have made a business decision to pause on offering the self-standing Thinair as we complete design work to streamline its deployment and integration with other component brands. The wind turbine will only be available as part of the drop-in hybrid power system PowerCrate®. PowerCrate is now available for as low as $70,000 (ex GST, freight). This guidance is valid for 2025
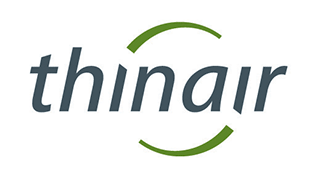
Wind Power Thinair 102 Turbine: Unique Benefits
The most obvious distinguishing feature of the Thinair turbine is that it only has one blade. This innovative and patented single blade is key to the unique benefits of the Thinair 102, and offers unparalleled advantages.
Traditionally wind turbines have been constructed with multiple blades all attached to a fixed central hub. The Thinair turbine, by contrast, has a freely teetering hub design that allows the blade’s angle to change in response to variations in wind speed. As a result, the Thinair maximises efficient use of strong and gusty wind by harnessing it to generate extra energy.
The teetering hub also protects the turbine from damaging stress, allowing the blade to swing into a safe horizontal park position in extreme wind conditions. This approach also creates less noise than the traditional angling of the rotor to the wind method used by most upwind machines.
Thinair 102 Horizontal Axis Wind Turbine Features and Benefits
Quiet
Most wind turbine noise comes from the blade’s tip and trailing edge. With only one blade, and running at a similar tip speed, noise is significantly reduced compared to a standard two or three-blade turbine. The single blade delivers significantly quieter operation without sacrificing generation capacity.
Longevity
In strong and gusty winds, the unique teetering hub allows the blade to respond to gusts, limiting stress on the turbine. If the wind becomes too strong, The Thinair 102 will shut itself down, with the blade fully teetered to protect itself.
Energy Capture
The angle of the blade is used to determine changes in wind speed and so maximise energy capture from gusts. The rotor can also be made lighter than comparative machines, which allows the turbine to be more responsive to strong turbulent wind.
Elegant
The Thinair 102 will be a design enhancement to your home. Part of the look of the turbine is the integrated fairing around the tower, protecting the blade from downwind turbulence and fatigue. Elegant and attractive, this wind turbine is a product that you will aspire to own.
easy to own
Thinair’s integrated electronic and mechanical systems ensure completely automated and hands-free operation, during both normal and extreme wind events. Inbuilt reporting of performance allows you to monitor the turbine.
domestic scale
Thinair 102 is designed to deliver from 3250 to 5200kWh per year on sites with average wind speeds of 5 to 6m/s. This will power all or most of the energy requirements of a well-designed house. A successful installation will require a site of at least 0.4 hectares (1 acre).
economical
Because of its simple design and one bladed rotor (blade costs are a significant factor in the overall cost of any turbine), the initial cost of ownership will be less compared to other similar specification turbines.
Horizontal Axis Wind Turbines
Wind turbines commonly have three blades that rotate around a central hub on a horizontal axis. Powerhouse Wind has applied innovative technology to the revolutionary new design of its Thinair Wind Turbine.
Built using only one blade instead of three, the noise generated by the Thinair wind turbine is dramatically less than its multiblade counterparts. The simple design of the Thinair turbine has reduced the level of componentry, compared to other similar turbines, reducing the cost and allowing a more competitive purchase price.
The ThinAir wind turbine has been carefully designed to be the perfect balance of energy generation, cost and fatigue life.
A Thinair turbine on a good wind site is a great complement to PV in New Zealand conditions. It is far less seasonal than PV, will run 24 hours per day if the wind is blowing, and turns a grey windy day into another energy generation opportunity. Our windswept New Zealand countryside is known for being one of the best locations in the world for wind power.
Wind Power is perfect for an off-grid system, and is also possible as a grid connect solution. Wind power is intermittent and must be replaced by other sources of power during periods of low wind.
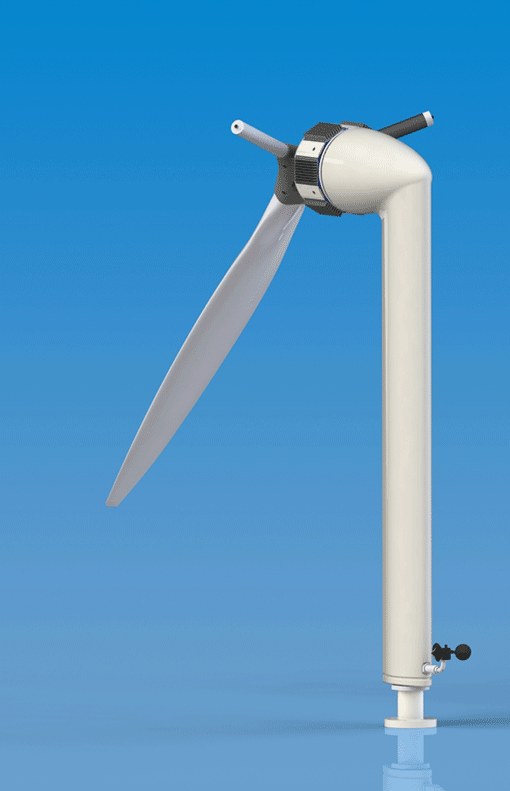
Blade in normal operation mode.
Teetering hub changes blade angle to maximise generation from wind gusts.
Hub teeters 90 degrees to protect the blade in storm conditions.
The addition of two equi-spaced counterweights balances the rotor and allows the machine to operate dynamically. It has the stability of a three-bladed wind turbine while maintaining the advantages of a single blade.
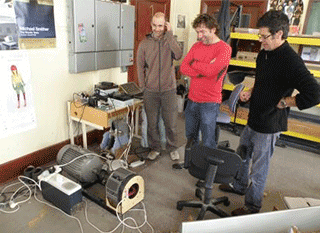
The creative clutter: Coaxing the systems to life. Left to right: Peter Shaw, Richard Butler, Wayne O’Hara.
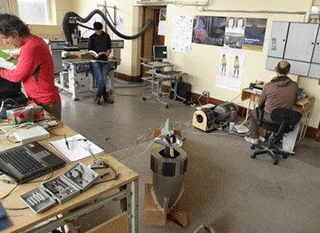
The result: Simple and elegant – and the perfect complement to PV. Innovative single blade and teetering hub design offers quiet, efficient and affordable home energy.
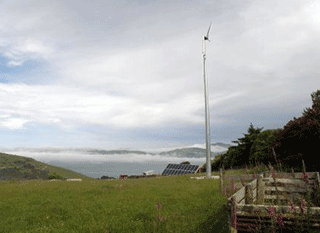
Thinair in normal operating mode Blade fully teetered in extreme winds.
Why One Blade?
That's the question that asks itself when you first see a Thinair turbine
Common sense seems to say that it can’t be possible to generate the same or more power with just one wing than would be possible with two, three or more, why not thirty?
Interestingly, common sense and physics are not always in perfect alignment, and when that happens it is usually physics that prevails.
The answer to this question from a performance point of view lies in how wind behaves as it passes through the rotor disk. The first step in understanding this is to take away the question of the number of blades altogether and think of what is called an ‘actuator disk’. This theoretical device is a circular disk that lets the student of wind turbine performance offer a variable blockage ratio to the incoming wind and harvest without loss, the energy that is given up by the wind as it slows down. As wind passes through the disk and slows down, the stream has to diverge and spread out to maintain continuity of mass flow. There has to be some optimum ‘slow down’ factor so the wind still flows away downstream (you can’t stop the wind) but equally if you don’t slow the wind enough you lose energy recovery.
It was first established by Albert Betz that if you adjust your actuator disk so the downstream velocity is 1/3 of the upstream velocity, you have found this optimum. See Wikipedia for the explanation and derivation if you want to follow this.
Betz also showed that assuming no drag and ideal performance from the disk, the maximum recoverable energy in a wind stream is 16/27 (or 0.593) of the incoming kinetic energy in the wind. Once this framework is established, we can turn to designing the best possible real rotor to replace the actuator disk. As a designer, we can choose many blades, fewer blades, what are the effects?
The blockage created by a rotor depends on the number of blades, the width of the blades (chord), the rotation speed of the rotor, the lift and drag properties of the airfoil sections chosen in the flow conditions they see. If we go for a lot of blades, we find in order not to block the wind too much, we need narrow section blades (small chord), at a low rotation speed. This is typical of the water pumping turbines associated with the American West.
They are great machines and often tick along for decades after they have been abandoned, and as slow speed machines, they produce a lot of torque (turning force) which works well for operating a pushrod water pump. They do however create a lot of rotation in the wake, which is energy not being recovered, and their overall efficiency is very low. As designers have wanted more efficiency, and higher speeds to drive generators, they have moved to use fewer blades, of wider chord and turning faster.
Following this sequence, many designs have stopped at 3 blades with the tip speed ratio (the speed of the blade tip divided by the speed of the incoming wind) taken as high as is possible without becoming noisy. 3 blades also have the useful property of having the same rotational inertia about the turbine yaw axis (the one that aligns it with the wind direction) no matter what angular position the blades are in.
This last point is not true of two-blade (or 1 blade 1 counterweight machines). The rotational inertia about the yaw axis is different when the blade pair is horizontal compared to vertical which leads to issues when yawing
while running for both free and powered yaw machines.
We decided to investigate keep going not just past three blades, but also past two, to just one. What effects and benefits could we find by doing that, seeing we were starting the design from a clean sheet of paper?
First, we realized from Betz that we either had to go faster or wider with our single-wing than an equivalent two or three-blade design to get the right wind slowdown. Faster is attractive in terms of making the alternator lower torque and thus smaller but runs the risk of being noisy compared to the competing designs.
So wider at a similar speed with high-performance airfoils seemed to be the right path.
In theory again, for single-wing design compared to three blades, there is about a 6% loss in energy recovery for the same flow conditions. Doesn’t seem too onerous – a little bit longer seems a small price to pay for only having to make one compared to three – but wait – the flow conditions aren’t the same.
Our design is running at the same speed as a competing equivalent 3 blade design, but with a much wider and thicker (bigger chord) wing. There is a very important ‘dimensionless number’ called the Reynolds number (again see Wikipedia for the detail) which is an expression of the ratio of the inertial forces in a flow, divided by the viscous forces. It guides whether it is the mass effects of the fluid that are controlling the flow behavior or its ‘stickiness’.
In any flow situation as you increase the speed and scale of a flow, there is a transition between laminar flow (dominated by stickiness) and turbulent flow (dominated by mass). The transition is a place to avoid, as it is unpredictable, random and messy. For an airfoil the Reynolds Number (or Re) is defined as u.c/v, where u is the flow velocity, c is the chord of the airfoil and v is the dynamic viscosity of the fluid.
It turns out that small wind turbines are operating in a range where transition effects are important, and getting the Reynolds number up makes a big difference to how the airfoils perform. By going from 3 blades to one in our concept design (at the same tip speed ratio) we go from Reynolds numbers in the 200,000 range up to 600,000. This sounds a bit esoteric, but it makes an important difference to the lift to drag ratio of the airfoils, and also the smoothness of the stalling performance. This picks up that 6% again and a bit more, and puts us in a good position for the design, getting performance that is better than 3 blades with just one wider and thicker wing.
It still leaves some important questions for the concept, and more benefits to explore. First, of course, at least one counterweight is needed, and when you look into the dynamics, a teeter bearing (like a see-saw bearing) is needed so the unbalanced aero force doesn’t go into the shaft.
With one counterweight, we are in the zone where yaw problems will occur, so we thought about options to fix that and investigated 2 counterweights to give three rotating masses. Not only are the yawing problems removed by that, but the rotor assembly with the right detail design, is free to teeter to any angle in a 180-degree range, and we could see an advantage to allowing the wing to ‘park’ to horizontal in winds above the running range for a high survival wind speed.
We have also extensively investigated the aerodynamic performance of our realized blade design, which is very detailed and uses 3 airfoils through the root, mid-section and tip regions. The University of Otago, principally Dr Sarah Wakes, has provided invaluable expertise in guiding student projects which have used computational fluid mechanics (CFD) to investigate the running and stalling performance of the Thinair blade.
The papers that have come out of that research are good reading for anyone who is interested in knowing more about the aerodynamic performance of the Thinair design. The Modsim paper is a good starting point.
Materials
The blade is made of Hi-Tech carbon fibre construction. The Chassis is made from a mix of carbon fibre and fibreglass.
Lifespan
The turbine prototypes have been operating now for over 5 years, the turbine is expected to last for up to 20 years. The turbine has a 3-year warranty.
Cost
Powerhouse Wind have established a recommended retail price of $17,100 + GST + freight.
Output
The turbine alone can generate an annual energy output, at an average wind speed of 5 meters per second of 3250 kWh per year.
Start The Conversation
Talk to us today about how we can help you with your renewable energy needs.